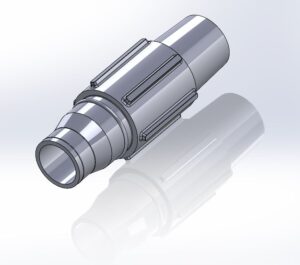
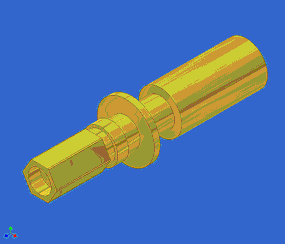
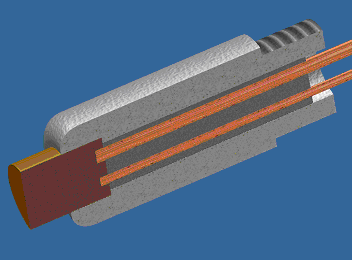

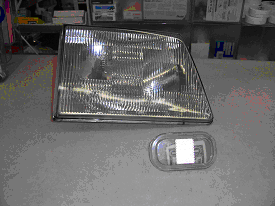
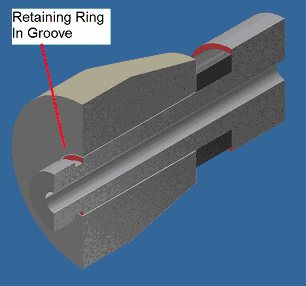
US PATENTS
6059483: Sealed joint for a multi-component injection molded automotive lamp assembly.
6395201: Method and manufacturing an automotive reflector.
Not patented yet in the US, but published: A Method For Producing Carbon Black Using An Extender Fluid. Note this has been patented in multiple foreign countries.
DESIGN AND ANALYSIS
- Decreased chemical process variation and nozzle replacement frequency by launching new spray nozzles with improved hardening treatment.
- Designed new composite part to eliminate ergonomic issue in manual process; improved quality, reduced cost.
- Eliminated quality and ergonomic issues by redimensioning components to reduce tolerance stack-up
- Designed and analyzed plastic mechanism for caskets to eliminate steel components from design.
- Designed custom injection-molded plastic housing and mounting features for Lego truck sound device.
- Redesigned line of failing plastic filter housings; new design exceeded fatigue life specifications by over 100%.
- Redesigned rotationally-molded coolant tank; reduced cost by 15% and eliminated four separate pieces.
DESIGN FOR MANUFACTURING AND ASSEMBLY
- Led Design for Assembly effort to reduce labor costs in new generation of electro-mechanical capital equipment, saving over $5 million in L&OH within three years of launch and reducing assembly floor area needed over 50%.
- Solved O-ring roll out problem in manual assembly operation through proper chamfer design. (Also discussed in the second part of this essay.)
- Recommended widening glue track to increase process window over 150% without compromising joint strength.
- Eliminated product’s 50% rework rate in brazing operation by redimensioning joint for proper process window.
VALUE ANALYSIS / VALUE ENGINEERING & COST REDUCTION
- Conceived, researched, and prototyped integrating heat shield functionality into plastic housing to eliminate separate-piece heat shield. Projected corporate-wide total cost savings of approximately $750K annually.
- Saved over $250K annually by replacing molded virgin rubber with superior material based on recycled tires.
- Examined molded-in reflectivity to eliminate process steps in automotive taillight manufacturing. Process had functional potential but cost savings did not pan out. (Presented to highlight creativity.)
PROCESS DEVELOPMENT AND PROBLEM SOLVING
- Co-invented “Integrated Molding and Assembly” technology. First application in modular cell; plant-wide labor savings potential over $500K. Technology was patented in 2000.
- Prevented machine damage by using laser scanning and data analysis to detect pattern in radiator fin heights.
- Saved over $150K in scrap/throughput costs by examining leak location. Supplier part was blamed for leak test failures; data indicated part was fine 90%+ of the time, and poor seating during assembly was creating the leaks. (Discussed as one example in this essay.)
- Identified root cause of water entrainment in headlights appearing at customers’ assembly plants, invented containment action, and verified permanent solution. (Discussed in this essay.)
- Discovered failure mode of high-end plasma torch returns from the field; analysis by the team dropped field returns by over 90%. (Discussed in the first half of this essay.)
- Identified shipping & handling as source of puncture failures in disposable sterile syringe blister-packs. Proposed tool and / or material change with pros / cons for each. (Discussed in this essay.)
- Enabled material change saving over $200K annually by proposing surface treatment to improve adhesion. (Discussed in this essay.)
PROJECT MANAGEMENT & BUSINESS SKILLS
- Developed and managed project plan for Lego toy truck and launched on schedule. Lego liaison called plan the “most comprehensive” he’d seen.
- Created process development prioritization list through QFD analysis.
- Prevented low ROI mold purchase by analyzing NPV of projected savings as a function of two key variables.
FIX THE PROBLEM
Fix the Problem I: Eliminate Variability, or Adapt to It – Case study of identifying where variation in a process comes from, and how to handle it.
Fix the Problem II: Medical Blister-Pack Punctures – Case study of finding the location of where a customer-found problem originated, and some proposed solutions.
Fix the Problem III: Ink Adhesion to Plastics – Case study about adhesion to plastics, and how it was solved.
Fix the Problem IV: Water Ingestion into a Headlight – Case study examining a problem at an OEM customer.
Fix the Problem V: Cultural Awareness is Critical – Case study of how an understanding of Japanese culture avoided costing people face.
Case Study: Choosing Plastics for a LEGO Toy Truck – Case study about how to select plastics for an application from my career.
Design for Assembly: A Child Sippy-Cup Cap – Case study of a DFA problem showing how partial symmetry can be a problem.
Fix the Problem VI -The Role of Material Microstructure in an Overmolding Application
Choosing Plastics – Why it’s important to think of the end goal – minimized part cost – and not obsess over price per pound of resin pellets.
Visiting Suppliers – Three examples of why visiting suppliers, whether prospective, established, or best-in-class, is a very good idea.
Fix the Problem VII: Product Launch Crisis – Case study about a product launch going particularly badly, and how we worked to identify the critical areas to focus attention.
Fix the Problem VIII: The Problem Toggle – Two examples of solving a problem by truly understanding the root cause… and how I found those root causes.
Fix the Problem IX: Three High-Scrap Issues on a Product Family – Tracing the root causes and eliminating the scrap on three different automotive radiators.
Fix the Problem X: Learning from Interview Problems – Three short case studies of problems I was presented with in interviews, as a part of seeing how I approach problems.
Fix the Problem XI: The Measles Chart – A very simple graphic, used as a first-pass data collection scheme in production trouble-shooting, can reveal tremendous amounts of useful information.
Lean Manufacturing: Weighing Theory vs. the POF – Lean Manufacturing in Theory and Practice, with a case-history overview.
Fix the Problem XII: When Chemicals Attack – Three short examples, with lessons-learned, about when chemicals attacked products and/or equipment.
Fix the Problem XIII: What’s Different, What Changed? – One of the key parts of production problem-solving is understanding what might have changed from good to bad, and how good parts differ from bad parts.